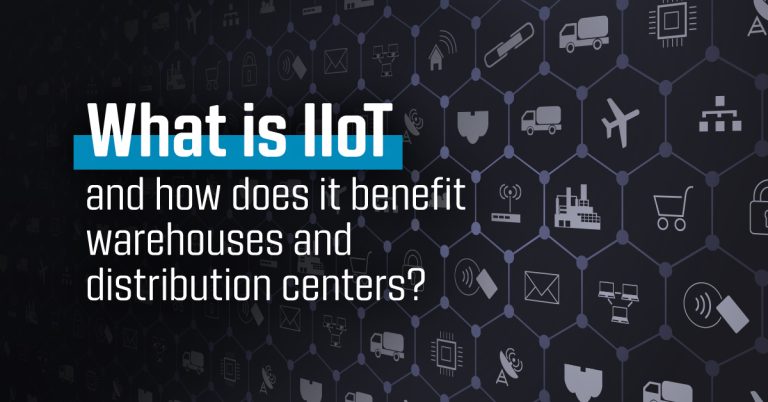
What is IIoT?
Technology is currently experiencing its Fourth Industrial Revolution, sometimes known as Industry 4.0. Where Industry 3.0 introduced computers, 4.0 is about connecting those computers so they can make decisions through artificial intelligence rather than human input. A vital part of this process is the Industrial Internet of Things (IIoT).
IIoT is an application of the Internet of Things (a massive network of smart devices that collect and share data) within industrial settings. This includes logistics procedures in supply chain management and warehouse automation, such as through the use of robotics. In fact, as companies continue to recognize the value of IIoT-enabled robotics, this “Internet of Robotic Things” market has grown at a massive CAGR of 29.7% from 2016 to 2022.
How does IIoT work?
While IIoT sounds very complicated, the process can be broken down into four simple steps:
- Using a variety of sensors, smart devices collect and store real-time data like temperature, quantities, and equipment wear from your assets.
- That data is sent through an internet network to an analytical application.
- The application then processes raw data from all connected smart devices, and uses machine learning to produce valuable insights for optimizing efficiency and productivity.
- Managers or employees use these insights to improve and grow their business.
The main difference between the data gathering ability of humans versus IIoT is speed. IIoT collects an immense quantity of data from many different sources in an instant. Then, its artificial intelligence and machine learning algorithms analyze in milliseconds what would take a single person years. This real-time visibility and understanding of assets means businesses can make relevant and informed decisions to streamline their operation.
What are the main benefits of IIoT?
Fundamentally, IIoT empowers businesses to:
- Redirect skilled labor into more profitable activities by automating menial tasks.
- Identify areas of operational inefficiency that limit production capacity.
- Avoid asset downtime by performing predictive maintenance when needed.
- Create new revenue streams by analyzing performance or usage data.
- Enhance product quality with more accurate quality control procedures.
As a result, IIoT-connected enterprises can boost their operational efficiency, reduce costs, and raise their productivity, all without investing more time or money. This in turn fuels expansion and growth.
How does IIoT benefit warehouses and distribution centers?
One of the most significant ways IIoT devices have supported industrial success is in supply chain management. As global demand continues to grow and labor shortages slow production, the automation of warehouses and distribution centers has kept the industrial sector afloat.
All the general benefits of IIoT also apply to warehouses and distribution centers. However, there are plenty of specific advantages to introducing IIoT to this stage of the supply chain.
Predictive analysis for stock management
Nothing is more debilitating for the supply chain than running out of materials or supplies. Some can take months to replace, meaning production grinds to a halt. And if you can’t meet your clients’ needs, they’ll find someone who can.
But the machine learning algorithms of IIoT devices can track the amount of stock you need based on usage habits over time. Then, when stocks reach a certain threshold, an automated order process can be activated to replenish them. The devices’ artificial intelligence system can even track the effect of market trends on your operation, allowing you to adjust to subtle changes in supply flow. That means you save significant time over manual stock management, and enjoy a seamless operation that never slows down.
Reduction in labor costs with autonomous guided robots
While the human body was built for manual labor, it has physical limits. Workers get tired, are prone to making mistakes, and are always at risk of illness or injury. So, instead of putting your human employees at risk, you can retrain them for skilled positions and allocate IIoT-equipped autonomous guided robots to handle the heavy lifting.
Now, a single person can manage a team of robots, massively increasing your throughput potential. These robots can avoid unfortunate accidents with their vigilant sensors and monitors, and calculate the quickest routes through the warehouse or distribution center to minimize time spent moving between tasks. Implementing warehouse automation using a fleet of guided robots can reduce labor costs and raise productivity at the same time.
Optimized use of floor space
The amount of stock you can carry at once depends on how you lay out your facility. Simply by rearranging your assets, you might find a huge amount of unused space becomes available.
Using an IIoT-enhanced warehouse management system, you can ensure you’re using your available space in the most efficient way possible. This also allows you to accurately track the entry and exit of goods, and to identify vacant areas where you can store further materials. That means you can improve your management of the supply chain, and take on more business without investing in additional facilities.
Easy tracking of assets
Warehouses and distribution centers handle a huge quantity of goods. And with so many delivery vehicles, items, and workers coming and going, it’s easy for assets to be misplaced or lost.
The monitoring potential of IIoT devices gives warehouse managers unparalleled visibility of their inventory, and lets workers locate stock quickly and easily. Tracking assets in this way also makes it easy to spot bottlenecks in your supply chain, and take action to increase efficiency and reduce costs.
Harnessing the benefits of IIoT with automation software
Although the introduction of IIoT devices into a warehouse or distribution center can have a profound impact on productivity, many of these function on surprisingly simple software. Take stock management, for example. By tracking how many items you typically ship at different times of the year and comparing this to larger demand statistics, it can make a reliable estimate for how many items you need. In many ways, the only differences between this calculation and a high school math class are the size of the numbers and the speed at which they’re processed.
But the same can’t be said for the use of logistics robots. Since these machines relieve workers of manual labor tasks, they need comparable visual, motor, and logical thinking skills that demand much more complex automation software.
In the case of picking and packing goods in a mixed pallet, a logistics robot needs to do three things:
- Process visual information to decide where to pick an item.
- Decide where to place an item.
- Quickly and accurately image package items and types in such a way that it can grab, lift, and place the package without damage.
To achieve these goals, the robot requires the superfast vision and precise hand-eye coordination skills provided by high-power vision software like Plus One Robotics’ PickOne. By combining 3D- and artificial intelligence-powered perception, our software enables logistics robots to perform picking and packing tasks with speed, care, and accuracy that far outstrips a human. This vastly accelerates the process, allowing any e-commerce warehouse or distribution center to transport a greater volume of products within the same time frame.
But this alone doesn’t account for one of the biggest misconceptions warehouse managers have about robotic automation: that they don’t make mistakes. In fact, no robot on the market today is able to perform its tasks flawlessly, even with machine learning capabilities. That’s why it’s necessary to keep a human in the loop with remote supervision software like our Yonder suite for robotic applications.
Yonder links to and communicates with logistics robots through the IIoT. When a robot isn't sure which action to take next, it contacts a human supervisor - who we call a Crew Chief - for guidance. It then employs its machine learning algorithm to remember the solution so it makes fewer stops in the future. Since a single Crew Chief can support a large number of robots through IIoT, the delays inherent to even the most advanced picking and packing robots can be swiftly neutralized.
Power your logistics robots with industry-leading automation software
IIoT devices give you the means to expand your business at pace. But when it comes to more complex machines and robots, they’re only as effective as the software you install.
For automation software that gives your robots top-class flexibility, accuracy, and intelligence, contact us today to arrange a free PickOne or Yonder demo.